The DEI (Department of Information Engineering) of the University of Padua (UNIPD) is the scientific coordinator of RIR IMPROVENET. The DEI, which currently has about 100 tenured professors and researchers and more than 50 fellows engaged in extremely broad disciplinary and research areas, is active in the following research areas: Automation, Bioengineering, Electronics, Computer Engineering, Applied Optics, Telecommunications.
Why does the University participate in the coordination of a RIR?
The RIRs were created by the Region to meet the research and development needs of local companies, and the Region itself wanted a significant presence in the same universities as UNIPD, which are at the frontier of research in the areas covered by network activities. In addition, universities have great experience in the participation and management of collaborative projects and can therefore make an important contribution both to the scientific coordination of network activities, and to specific project initiatives.
What is the added value of IMPROVENET?
UNIPD with the DEI offers a know-how of excellence with regard to all information technologies (ICT), both in terms of technological approach and methodological. Furthermore, at the strategic level, the presence of DEI can facilitate the activation of wide-ranging collaborations, such as the European one, in line with the main vision of the Region.
What are Regional Innovation Networks for?
Networks play an important intermediary role, in particular as regards the transfer of knowledge (and not just technology) between the research world and the territory, and in this sense the presence of UNIPD is perfect in line with what is called the Third Mission of the University. UNIPD has found in the IMPROVENET network local companies with a great vocation for innovation, with which it was natural to start research activities.
The role of industrial partners is crucial in applied research, as they provide expertise and infrastructure in a wide range of fields which are difficult to replicate in university research laboratories. Therefore, companies become a kind of expansion of the research capacity of the university, playing the role of advanced laboratories where to test innovative methodologies and technologies developed within the universities.
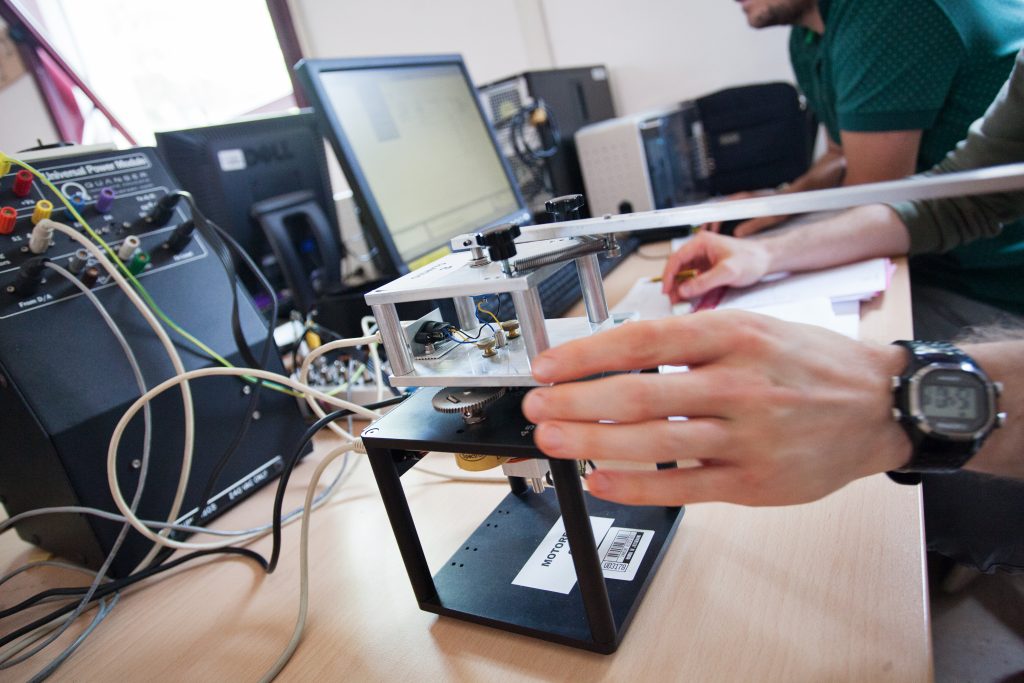
What is the VIR2EM Project?
UNIPD is the scientific coordinator of VIR2EM and is also involved in the development of systems and processes models for the digital twin and the use of artificial intelligence methodologies for the development of monitoring tools, supervision remote control and optimization of service and after sales operations.
The research activities are carried out in collaboration with colleagues of the University of Verona, for issues related to digital twin, and with some companies of the partnership (Sperotto Rimar for modeling activities, Galdi and Statwolf for prognostics, diagnostics and maintenance with machine learning tools).
With the previous project PREMANI, UNIPD has carried out research activities focused mainly on the development of predictive maintenance algorithms on products and processes, in collaboration with Elettrolux and Galdi.
What future awaits RIR IMPROVENET?
We expect an increase in the activities related to the Network, especially considering also the next investments related to PNRR and the new regional programming. We also hope to have a network of companies increasingly alive and active, with which to project Improvenet beyond regional borders, with the ambition to play an important role in representing the extraordinary industrial fabric of Veneto at national and international level.
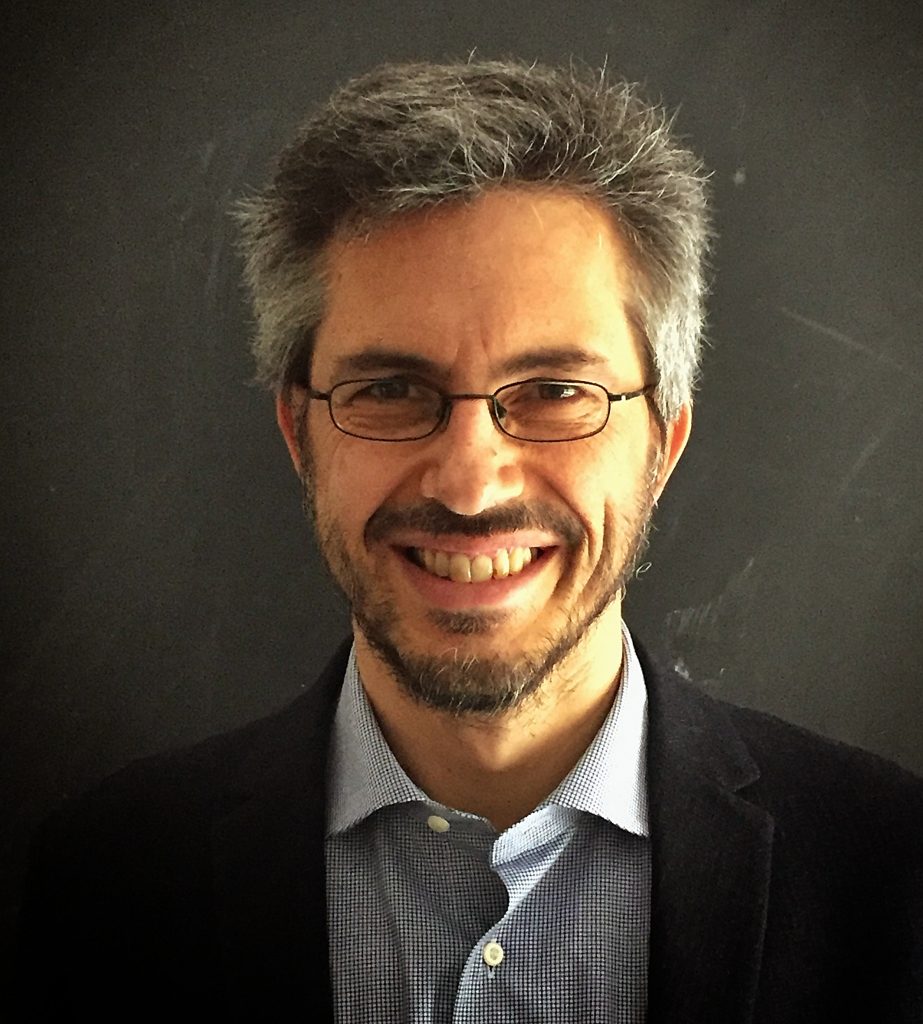
Prof. Alessandro Beghi
Alessandro Beghi (Ph.D.) is Full Professor of Automation at the University of Padua. He holds various positions at department and university level, in the areas of technology transfer, research, and intellectual property management. He has been a visiting scientist at international universities and research centers both in Europe and in the United States. He is a senior member of the IEEE. He served in the program committees and organizers of many international conferences. His research interests include modeling, simulation, identification and control of complex systems, and their applications in different scientific and industrial fields. He was responsible for research projects funded by the European Union, the Ministry of Education and Research, the University of Padua. He has been responsible for research activities with national and international companies, including Electrolux, Emerson Network Power, Infineon, Aprilia Racing, Ducati Corse. He is co-inventor of 7 patents on the use of advanced control techniques in different application fields. He is the author of over 200 publications on magazines, books and conference proceedings.